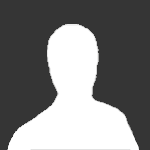
More C-125 / K301 questions with photos...
By
Jeff-C175, in Wheel Horse Tractors
-
Similar Content
-
By BrianKoch
Gentlemen,
I am in need of help. While doing yard work with my K301 powered ‘68 Charger 12 it suddenly came to a stop and won’t start again.
My troubleshooting so far:
Fuel:
• stabil/87 and clean
• good flow before and after pump
• carb clean, recently rebuilt, float level correctly set
Compression:
•good? - blows finger off spark plug hole
•good turnover but doesn’t fire off
•piston and cylinders move freely
•valve lash set .008 intake .018 exhaust
•breather assembly correct and recently serviced with new gaskets and filter
•head gasket not broken, head bolts tight, some carbon on head
Spark:
•no spark
•all electrical/ignition components were replaced 1 year ago except voltage regulator
•no loose connections, no grounding connections
•inspected and applied graphite to starter shaft
•changed plug
•12v to coil good
•cleaned points, points wire has continuity
•condenser ground good
•swapped battery, points and wire, plug and wire, coil, and condenser from running K301 (‘69 Charger 12)
•points push rod does push out when turning engine over by hand, but unable to get points timed using multimeter method and timing mark on flywheel
What else should I check/do?
-
By BrianKoch
Looking for a good and flat cover plate for the k301 crankcase. My current one is warped causing oil to leak out.
-
By RORY K.
nice tractor for resto runs and operates blades need replaced.little tlc all it needs.
-
By Tuneup
Hi all,
Summary: Solid mounts a year ago were very nice. Removed balance gears last December. Unacceptable. Installed eBay originals in good condition. I can ride it again at full throttle AND keep my fillings.
Long story (I have the day off):
A thread inspired me last December to look and see if my balance gears were doing well and the rear one was a wobbler. Removed them. She was burning too much oil - original rebuild was just a stone hone and power was not as it should be - it took months to get it bored .020. Hard to find in GA. Installed everything and started her up. Solid mounts USED to be great! That old off-idle vibration that shook the hood was gone thanks to those mounts. A little more vibration was OK. After the removal of the balance gears - NOT! The thing makes my butt numb and I can't mow at higher than about 2500 RPM. The hood vibrates just too much.
Decided to shop Flea Bay for some used, but OK, mounts. Toro prices are . . . the usual Toro prices. Mine were shot and tossed in the bin. Easily installed, right?
I thought in my ignorance that I could just remove a solid mount one at a time and pop-in the originals. Heck, the mount rubber has to be pressed in! Who knew? My old ones weren't like this at the restoration years ago.
Delayed while I figured how to pull the engine on my own. I used to just throw it up on the bench but I've grown more cautious. No buds around in the AM for assistance. Tied some 10 gauge wire around a 2x3. Put one end on the table saw and lifting was easy. Still have to lift the weight but no bending and it was going on the floor. Dead lift at knee level. Pulled the 2x3 across the table to extend the engine to the side of the tractor and let her down slowly.
Engine bay still pretty clean and the engine oil was due for its 1 hour drop after the rebuild anyway. Looked fine.
How to get those mounts in? Tried a C clamp and a socket as a spacer - too clumsy. Greased them up nicely and got longer bolts - tightening them a bit at a time and nudging the mounts into the hole with a blunt object. Turned out not to be a bother!
I've learned not to throw things away. It always seems that you need something the day after it's in the garbage truck. I still had the grounding lead and the large mount washers.
The wife assisted in the re-installation. Kinda' freaked her out. Back in place, and I got to clean the lower engine area from that minor oil leak around the fuel pump. Attracted grass clippings like a magnet.
A few bulb squeezes to start her up and, glorious! No more teeth chattering and I can take her up to 3600 if I like - sounds wonderful and she tore through the deep, deep crab grass. Don't discount those mounts. Sure, that off idle vibration is back and stronger than before. Nothing like a fresh bore for power. Something to spend time on tomorrow.
Now, what to do with these?
-
-