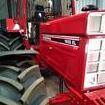
-
Similar Content
-
By T-Mo-(Moderator)
Sorry for the late notice, but if anyone is near Fredricktown, Missouri, the 17th annual Cubarama is being held this weekend, starting Thursday, the 27th, (set up day), Friday September 28, and Saturday September 29. It's held the last weekend of September each year in Fredricktown and is for the Farmball Cub and Cub Cadet, but basically anything IH related.
Fredricktown is about 80 to 90 miles south of St. Louis.
-