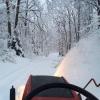
Auto 18. Help rewiring ignition after electric fire.
By
wheelhorse-c-161-1979, in Wheel Horse Electrical
-
Similar Content
-
By BuffaloD200
Hey all,
My '74 D180 has a lot of trouble pushing snow. Weighted tires, but nothing else at this time. I've found it gets stuck frequently and only one wheel spins. Do these tractors not have a limited slip/locker arrangement? How does everyone manage with the infamous one wheel peel?
-
By BuffaloD200
Hey all, I need to install a drive belt on my 75 D180 for my snowblower. I've looked through a bunch of D-series owner's manuals, and none seem to mention replacement procedure. The PTO pulley is fixed, save for engaging the PTO and there is minimal movement at the snowthrower pulley. There's no idler or tensioner as far as I can tell. Do I have to remove the PTO pulley? That seems to be a required service item.
Same question for my 80 D200 as well really.
Using the recommended 4L490W belt.
Thanks
-
By 953 nut
I have a few basic electrical system diagrams that are helpful in understanding how the wiring system works. They are not specific to any particular tractor and do not include safety switches. All use the 5 post ignition switches 103-991 for Magneto and 103-990 for Battery Ignition. I failed to include fuses in the Starter Generator drawing, this is an over-site and I would encourage fuses be used as shown in the other two drawings.
Hope this is helpful.
Magneto Ignition system with electric start and solenoid.
Battery powered ignition system with points, condenser, solenoid and electric start.
Battery powered ignition with solenoid, points, condenser, Starter Generator and a mechanical voltage regulator.
We have uncovered a shortcoming in the factory wiring diagrams for S/G battery ignition systems with a four terminal voltage regulator. The wire from the regulator "Gen" terminal to the S/G "A" terminal was omitted. This drawing should clear that up.
-
By ihatephones
I got a D-180 for $250, and the governor is messed up, the points won't open or close, and I took it apart and was being stupid and messed some stuff up in there, and now I need a new one.
Where can I get one that's not on eBay for $200?
I also forgot to say it was a Kohler K482, and I'll throw some pictures of the tractor in as a treat.
-
By Brandon Byers
I know I'm half a year ahead of schedule!
I picked this 1974 D-180 up early last year. It had a pretty hard life, and the previous owner gave his best attempt at keeping it alive. Hydro was strong so I serviced it and put it to work mowing all year. I decided if it would make it through the season then it would get some TLC. By fall it was burning about a quart of oil an hour but it made it. I have no clue how many hours are on it, every hole, bushing, bearing on this tractor is pooched. If you look closely, somebody used two 1" NPT Pipe Flanges to rebuild the mounting points for the upper 3 point cylinder. Hey it works!
I rebuilt the steering gearbox and re-bushed the front axle along with making new spindles.
I had the 482 Kohler bored .20 over (it was .10 over already) and gave it a rebuild with the intention of putting it back to work on snow duty.
I then dawned on me that this tractor will be 50 years old next year - and these old D's are becoming harder and harder to find anymore. So I decided to customize it a bit and go for what a maybe a dealership would offer for a 50th anniversary model if Wheel Horse was still in business today (In another universe, maybe!)
As D's aren't known for their looks - and I can't leave anything alone. I took approximately 2 Inches out of the grille and bezel.
I updated most of the wiring and lights. Gave it a new set of Carlisle Ags along with Vredestein front ribs. It got a new seat and I painted all the accents aluminum.
I patched, rebuilt the 48" deck and put new blades, wheels, and hardware on it. The Blade & 3 point scoop somebody adapted to it also got some attention.
Lastly I stripped it most of the way down and painted it with IH red acrylic urethane enamel.
I always forget to take pictures during my projects but here's a few:
Before:
After:
Thanks for reading!!
-