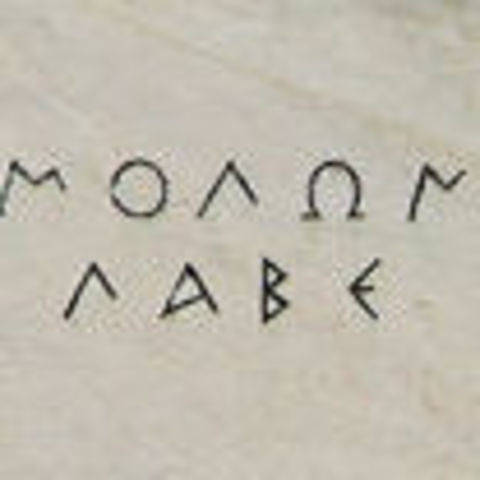
-
Similar Content
-
By ztnoo
Not sure this is in the right category, but here goes anyway.
I have a hydraulic fluid leak problem which originally WAS NOT particularly noticeable or troublesome.
Now is would be better described as a HEMORRHAGE.
Some of you may remember me doing battle a year ago last winter with the rear hubs on my GT 14 to originally correct an issue with one which had slid inward on the left axle.
In the course of that adventure, it was mentioned to me that might be an excellent time to replace my 47 year old axle seals.
They were leaking somewhat, but were not what I would describe as an emergency or huge fluid loss problem.
I decided since it was the middle of winter and I was messing with the hubs, the suggestion made perfect sense to do some preventative maintenance at a leisurely pace given the time of year.
So I was able to complete my horrific hub removal/woodruff key battle, but managed do the axle seal installation without major drama.
I had completely drained the tranny prior to axle seal removal and upon installing the new seals and a new tranny filter, filled with fresh Type A tranny fluid.
During the middle of the mowing season last summer, I began to note my hydro ground speed response was a bit sluggish and slow.
After checking the fluid level in the tranny, I noted it was low.
The system is a 4 quart system and it required over a quart to bring the fluid up to proper level.
I checked around a different locations of the hydraulic system for some obvious telltale signs of loss.
The new axle seals looked great, no loss there. The hydraulic cylinder looked OK from what I could tell after hosing the area down and running it again after cleaning. Didn't appear to be any significant or apparently loss there.
The hoses looked OK with no cracking or splitting, and their fittings seemed to be leak proof.
However after running the tractor for a while in a stationary position and using the control valve which lifts and lowers the mower deck, I could detect leakage out of the top of the valve. The leakage was only coming from the top of the control valve in the area immediately below the valve lever itself.
My assumption is since I replaced the axle seals and stopped any fluid leakage in those two locations, potential leakage problems in the hydro system have migrated to the next weakest point.........in this case the control valve (#8363).
Unfortunately, I did not attend to this problem last winter as I should have (DUH!), being aware of the problem.......which of course continued the remainder of the last mowing season.
So..........guess what? The problem for some reason has not resolved itself without my engagement over the winter. And now its mowing season.......and in the two mowing sessions I've done since getting my mule drive problem and deck gauge wheel axle support problems resolved after running over a 3/4" steel form stake, the leaking/hemorrhaging control valve seal is only getting worse. I once again added over a quart of Type A fluid before my first mowing this year to bring the fluid to proper operating level.
I know it needs fixed meaning new internal seals need to be installed. The problem is how to get to the control valve to remove it or manipulate it in some fashion to install the seals on the spool valve and get it reinstalled in the control valve body without tearing the tractor half way apart.
Lots of older WH tractors have the hydraulic control valve on the outside of the hood stand or some side area of the tractor generally on the left just forward of the the seating position and under the dash area, which would make servicing the spool valve a relatively simple procedure.
Not so with the GT 14.
The control valve is located between two tall, heavy gauge "C" shaped steel panels which sit on top of the frame rails.The hood stand mounts to these "C" channel members. There is about 5 1/4" of width between the C channels......not a lot of room for a guy with big hands and fingers to operate.
My primary question is can the control valve and its primary operating part, the spool valve which has two seals, be serviced without completely removing the valve body from the tractor???
Is it possible to manipulate the valve after removing the mounting bolts from the right side C channel in such a way to gain access (the spool is removed from the bottom side of the valve body by removing a snap ring), either from the top or the bottom of the tractor to successfully remove the spool valve from the valve body, replace the seals, and reinstall the spool valve in the body of the valve without removing all the hoses and completely removing the valve from the tractor?
Without the tractor running, will there still be residual hydraulic pressure in the lines and in the system in general which would cause fluid to spurt out once a component is removed.........a hose or the spool valve itself for instance?
The control valve is WH part # 8363 and I see that Lowell Scholljegerdes (wheelhorseman1000) has a seal kit for resolving this leakage problem with "Control valve seals #7788". The seals are very reasonably priced and readily available and will undoubtedly fix the tremendous leakage at the top of my control valve.
https://www.wheelhorseman1000.com/product-p/00123.htm
The problem is what all is involved to get to the valve for the repair and how long something like this might actually take to get the tractor back in service?
One of my big concerns is the hoses which are now 48 years old. They show no signs of leakage now, but I fear if I start manipulating and moving them around too much messing around with the control valve, I'll create a whole new dilemma.
The big problem is its right in the critical time of year for mowing season here in Indiana, and with the mass quantities of rain we have had the last week or so, once it turns 75 or 80 or more, I'm going to need to mow twice a week just to keep up. Since my GT 14 is my only tractor and my prime tool for mowing, I just can't afford to have it down for a prolonged period this time of year.
If there's not a decently quick and reasonably simple removal procedure someone can suggest, I may just have to continue to keep the fluid level up in the tranny and control the mess of the leakage around the top of the valve as best I can until a drier time of year when mowing isn't a pressing twice a week issue. I might even have to just grin and bear it and keep adding fluid until mowing season is over in the fall. That assumes of course the hemorrhaging doesn't get disastrously worse than it already is.
I'm anticipating once this particular leakage issue gets resolved, the next weakest spot in the hydro system will show up, but first things first.
Any suggestions or words of wisdom anyone has to offer about this repair, I am completely open to listening.
Thanks,
Steve
p.s. I've attached a few pics below of the control valve and the affected area which is leaking for your reference.
leakage area circled
leakage area circled
*** Updated Addendum: June 1, 2017
See my last post dated June 1 on page 2 of this thread.
-
By ztnoo
I've been looking for a replacement small General Motors pickup from roughly 25 years ago in reasonable shape for 4-5 months.
After reviewing untold numbers of CL listings during the period, I ran across what looked to be a reasonable mileage example in good aesthetic shape within a reasonable driving distance from my location.
It was listed on CL in Louisville. Not exactly the next county over (a three hour one way drive), but a good enough prospect, I decided to take a day road trip
3hr 2min, 187 miles, per Mapquest.
I was thinking.......OK Steve, you are wanting to drive to Louisville to look at a vehicle, so what if I couldn't find anyone (a local friend/neighbor) available on Saturday to go with me?
Three strikes and I was out. Bingo. Reality sets in.
My theory was, if it was something I really decided I wanted, I needed to get it out of Louisville THAT day. But with no drafted co-driver, I had a definite problem.
In a eureka moment, I remembered Chaplain Manny, who I had never met, but with whom I have conversed extensively, not only here at RS, but on various WH FB sites, and by email as well.
Manny was raised in Louisville, so I instinctively knew he would be an excellent guide and pathfinder in a metropolis I had no familiarity with, other than passing through on I-65 to go to Florida.
So, I messaged Manny on Friday with my situation and proposal and asked if he would be available to assist me for a few hours on Saturday. He now lives east of Jeffersonville (across the river from Louisville, in Indiana) in a very small rural town.
He replied and told me he was available to help me, given his wife and young son were away at a wedding he wasn't attending.
I explained the situation generally, and to my amazement and luck, Manny agreed to help me go into Louisville on my long bed S-15 quest.
I arrived a little after 9 am at Manny's residence (following a three hour drive) and Manny proceeded to guide me into the bowels of Louisville.
Traffic was horrific for some reason on Saturday morning on both southbound bridges over the Ohio River into downtown Louisville. Manny speculated there had to be some big event going on downtown that morning, but we never did learn what it might be. I would have definitely lost my cool sitting and waiting for traffic to start moving and the stress of trying to navigate the unfamiliar interior of a major urban jungle. But Manny took it all in stride and we eventually maneuvered around the bottlenecks and we got to the desired address in an area of town known as Germantown.
So the short of it is, I bought the truck because it was in excellent shape for a 1990 model with reasonable mileage given its age, and Manny drove the station wagon while I followed in the S15 and we went back north across across the bridge over the Ohio River leading the way back to his place east of Jeffersonville. Generally speaking, the theory "move your feet, lose your seat" applies to CL items, because they can move very quickly and you usually have to have your ducks lined up and be ready to act promptly, or there's a high risk of losing your chance. With Manny's help and assistance, I was able to achieve my goal.
Manny let me park the truck at his house until I can draft a friend into a day road trip to go retrieve my little S15 jewel later this week. When we got back to his place and he showed me his Wheel Horse collection and ongoing projects and we philosophized about life a bit before I left.
Manny is a great caring and helpful person with a warm and outgoing soul. He has considerable health issues for a male of 56 years of age, but he does his best not to allow that to distract his quality of life and daily routine. I now consider him to be a friend and buddy and not just a correspondent........having met through our mutual interest in Wheel Horses, GT 14s in particular.
Steve
___________________________
Manny & me.
Manny in front of my purchase.
My "new" S15.
-
By ztnoo
I have a Kohler K341 on a GT 14 tractor.
Its always had the typical .....what are they called?........pepper shaker muffler? on the tractor.
I've had to replace them several times....they seem to just eventually burn up.
I can honestly say even from day one whenever I installed a new muffler of this type, I really couldn't tell that it really muffled much noise, maybe a little, but very little.
As usage time goes on, they all got nothing but louder.
Of course, part of this is the sheer displacement of the motor......35.9 cu. in. = 588 cc. Think of it in terms of a slightly bored out Norton Manx 500 cc thumper with an open megaphone exhaust. Deafening! You don't want to be standing 8 or 10' behind a Manx when it being warmed up and the throttle is being "blipped" to do that, without ear protection.
These older flat head engines seem to be much louder than the newer OHV engines which are common in lots of equipment now.
I've owned and used this tractor for 35 years now, and I guess I'm beginning to become somewhat of a crotchety old senior, but its becoming annoying to me (the operator), and I in fact had one neighbor that ragged me out over the noise.
It may be because they have a pool and spend a fair amount of time outside, and the pool is about 10-11 feet from a chain link fence that divides the properties.
I'm really not that worried about the neighbor nearly as much as I am myself, or should I say my hearing.
I already have hearing loss from years of firing pneumatic nail guns and listening to compressors and heavy machinery running on job sites.
What are you other K341 owners using and doing to get more muffling accomplished?
Surely there has to be a more reasonable solution which will allow you to hear yourself think after an hour or hour and a half of operation.
Is there a viable, positive solution for this problem so my ears and head don't ring for an hour after just mowing my lawn?
Regards,
Steve
-
By ztnoo
As many of you know, I've been in a prolonged battle with the rear hubs, woodruff keys, and oil seals on my 1969 GT 14, Model # 1-7441.
I'm to the point of installing the new SKF oil seals today as soon as I can round up one more PVC fitting to properly size it to my seals for tap in installation.
After that, its spin on the new NAPA 1410 hydraulic filter, and then fill with ATF.
When I drained the tranny, I measured and computed the volume of ATF taken.
It was right at 128 oz. + or - maybe two ounces. The volume spec says 4 qts. (4 qts. = 1 gallon = 128 oz.)
So I know I was within spec, and wasn't losing large amounts of fluid, although I have a couple of random minor seepage locations on the tractor.......mostly around the control value which raises and lowers the mower deck.
ATF is always what has been in the tranny, so that's what's going back in.
My reason for caution regarding what to use specifically is probably more a matter of jargon and my understanding of terminology than anything.
Of course, since my GT 14 was a first model year tractor, Type A transmission fluid was specified in all the literature.
Type A is no longer available, but it my understanding is that equates with Dextron II.
But isn't Dextron II now an outdated designation?
If so, what should I be putting back into this Sundstrand 90-2062 tranny to ensure continued adequate trouble-free lubrication???
I have more than a little angst over wanting to make sure I used the right product in this transmission.
The changes in products over the years makes it very confusing for those of us who only occasionally wander in and out of discussions like this and automotive/mechanical related jargon and word usage generally.
So gentlemen, what are your specific recommendations on tranny fluid to use in my Sundstrand, and is there any particular brand any of you favor over another?
Or is it pretty much the case that ATF is ATF is ATF, the world around?
Looking forward to your suggestions and recommendations.
Regards,
Steve
-
By ztnoo
I thought hub removal was taxing stuff, but its almost kid's play when compared to getting a frozen woodruff key removed from an axle still in a tractor.
After several days of attempting to remove the stuck woodruff key from one of my GT 14 axles by use of about every means known to me and maybe the whole of mankind, I've opted to attempt splitting the key in place in the axle.
I'm using a Dremel tool with a thin metal cutting disc and working at collapsing the remnants inward then punching the remains out of the key slot.
I'll get it done one way or another, but I'm going to have to source a new key and I'm thinking why not just replace both axle keys on the tractor.
The other one almost fell out upon hub removal, so I am being punished unmercifully on this second axle for unknown reasons.
My preference is to buy replacement parts locally when I can, but with these whopper woodruff keys I seem to be having some difficultly locating the proper replacements nearby.
They are rather large keys by my standards and brief experience dealing with this stuff.
I've miked the good key from the second hub removed: 1/4" (W) x .58" (H) x 2" (L) on a 2 3/4" diameter, full radius.
Where and from whom are small volumes (2-10) of woodruff keys of this and similar specifications available?
Who do you gentlemen recommend and order from?
Steve
-