Sign in to follow this
Followers
0
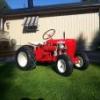
Front rims..
By
Lars, in Restorations, Modifications, & Customizations
By
Lars, in Restorations, Modifications, & Customizations