Sign in to follow this
Followers
0
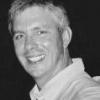
C161 with a K341AS - Turn to start & fuse blows
By
Highland Horse, in Wheel Horse Electrical
By
Highland Horse, in Wheel Horse Electrical