Sign in to follow this
Followers
0
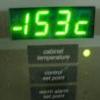
D Series Hydro motor gasket question
By
coldone, in Transmissions and transaxles
By
coldone, in Transmissions and transaxles