Sign in to follow this
Followers
0
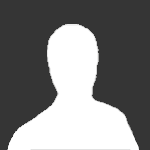
Hydraulic hoses - fitting sizes - etc.
By
Jeff-C175, in Implements and Attachments
By
Jeff-C175, in Implements and Attachments