Sign in to follow this
Followers
0
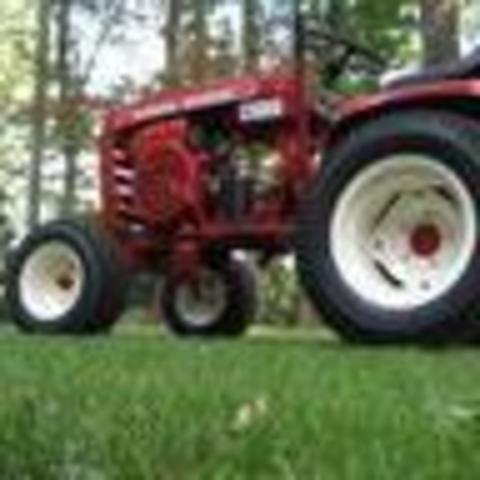
Snow Thrower Repairs - Welding Question
By
rmaynard, in Implements and Attachments
By
rmaynard, in Implements and Attachments