Sign in to follow this
Followers
0
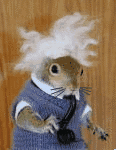
Metal skins paint preparation
By
Save Old Iron, in Restorations, Modifications, & Customizations
By
Save Old Iron, in Restorations, Modifications, & Customizations