Sign in to follow this
Followers
0
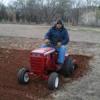
1985 416-8
By
Prater, in Restorations, Modifications, & Customizations
By
Prater, in Restorations, Modifications, & Customizations